F-theta lenses keep laser-scanning nice and linear
F-theta lenses have a laser spot position linearly proportional to the scan angle and are thus useful in many laser-scanning applications.
Laser scanning systems are used to scan a spot (or, with two scanning mirrors a line) or to accomplish laser-machining tasks such as drilling or cutting. Laser scanning mirrors, such as a galvanometer and polygon scanners, often produce a beam with a linearly changing angle theta. When a laser beam is passed through a normal focusing lens the spot’s position on the image plane will change nonlinearly over time. This results in variations of the received laser energy per area.
An “f-theta lens” is designed to solve this problem. It is so designed that the position of the point in the field of view scales linearly according to the input scan angle th of the lens. This means that the angle on the input side of the scanning polygon, or mirror, is directly proportional with the field position on output side. This property is valuable for any scanning system, whether it’s for materials processing or otherwise. A f-theta has a flat surface to accommodate the whole scan area.
The following is a sampling of various types of f-theta lenses and scanning systems on the market.
Telecentric or nontelecentric?
A telecentric f-theta has an additional feature: All chief rays are parallel to optical axis. The focused spot will not move if, for example, a metal plate is moved away from the focal plane. Telecentric lenses are heavier, larger and more expensive than nontelecentric ones. They should only be used if necessary (when the laser or optics could shift enough for the laser spot to go out of specification).
Sill Optics, based in Wendelstein, Germany, produces scan lenses for UV, visible and infrared lasers. You can also choose between optical glass and fused-silica lenses. The latter is often a more cost-effective option. Fused-silica lenses for high-power lasers are required. The low coefficient of thermal contraction and low dependence of the refractive index of fused silica on temperature result in a minimum thermal focus shift.
Different optical glasses are required to correct the lateral and chromatic shift in color for polychromatic lenses. These scan lenses are used in processes that require online observation and ultrashort pulsed lasers. Due to their shorter pulses, femtosecond lasers offer a wider wavelength spectrum than standard Lasers. One femtosecond laser pulse is powerful enough to damage lenses made of low-cost glass or internal reflections.
The S4LFT7012/292 polychromatic laser lens by Sill Optics was developed as part of the European Horizon 2020 research project ADALAM. The aim was to develop a sensor-based adaptive micromachining process that would measure topography online using a spectrometer and a scan lens.
The beam is split in two, a working beam and a reference one. The working beam passes through the scanning lens and is focused on the work surface. The reflected beam portion is used to measure topography at the spectrometer. A mirror also reflects a reference beam into the spectrometer. The wavelength difference gives information about the path length of the beams and therefore the height profile on the surface. 1). This measurement is similar to that of an optical coherence-tomography (OCT).
This application used an ultra-short pulse laser in the wavelength range 540-590 nm. This application requires a scan lens that is both ultrashort pulse capable and color corrected. A lens design that minimizes the lateral color shift (5 um here) and chromatic focal shifting (30 um here) was optimal.
The standard micromachining process with ultrashort pulse lasers is accurate and reproducible, but pockets that are hundreds of microns deep show significant errors. ADALAM’s adaptive laser process, which was developed and tested as part of the project, is a great solution to such challenges. A chip-breaker was made on a carbide drilling tool to test its effectiveness. Adaptive microdrilling increased depth accuracy by a factor of five compared to nonadaptive laser processing.
Wide range of wavelengths
F-theta lenses are used at wavelengths across the optical spectrum. II-VI (Saxonburg, PA) produces a portfolio of f-theta lenses that cover wavelengths from the UV to the far-IR (from 266 nm to 14 µm) for a wide range of industrial lasers, says Je Sun Oh, product line manager, microprocessing laser optics at II-VI (see Fig. 2). “II-VI’s f-theta lenses enable a variety of materials-processing applications including welding, cutting, marking, scribing or engraving of metals, plastics, carbon fibers, and glass,” she notes. “Other applications include laser surface treatments and additive manufacturing.”
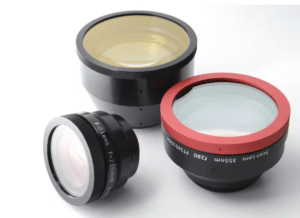
F-theta lenses keep laser-scanning nice and linear
II-VI combines zinc sulfide multispectral optics with fused-silica optics to achieve small and light scan lenses operating at a 1 µm wavelength that enable faster OLED film cutting with fiber lasers, says Oh. The company also developed a housing design to seal scan lenses and achieve very high transmission at a 5 µm wavelength, enabling curved cutting and fine microdrilling of glass panels with carbon monoxide (CO) lasers, which operate at around 5 µm.
Micro- and macromachining
Industrial applications require components that are industrially hardened, as well as that have the ability to be swapped out quickly. “F-theta lenses from Jenoptik fulfill the requirements of almost all standard methods for micro and macro laser materials processing,” says Dr. Maria Oliva, Director Global Product Management Semiconductor & Advanced Manufacturing at Jenoptik Optical Systems. “Our product portfolio includes f-theta scan lenses for almost all common wavelengths and geometries [see Fig. 3].” Oliva notes that the lenses do not require additional cooling, even at high laser powers.
Oliva says that the adhesive-free mounting technique also ensures long-term stability and investment security. Each lens is tested for transmission, cleanliness and performance. Jenoptik lenses of the same type can be replaced for applications that call for a lens replacement without requiring major laser system adjustments. Each f-theta is equipped with a protective glass that can be replaced individually.
A wide variety of laser applications can benefit from the company’s new 355 nm telecentric ftheta lenses. The short lens focal length allows for a small diameter spot in a scan area of 22 millimeters. Spot sizes up to 4.5 millimeters can be achieved depending on the application. Oliva explains that Jenoptik has developed a mounting technology with high accuracy for precise adjustments. It is optimized for micromachining in the microtechnology, electronic, and display markets. The very small telecentricity allows for unprecedented accuracy and quality of application. The lens’s high telecentricity and small spot size make it ideal for drilling high-accuracy holes in printed circuit boards, including via-hole drilling. This large scanning field allows for an increase in throughput.”
Systems with f-theta lenses
Scanlab (Puchheim, Germany) is a company that does not manufacture scanning lenses itself, but instead integrates scanning lenses, including f-theta lenses, from various manufacturers into complete laser systems produced by Scanlab.
Florian Merkt is a systems engineer at Scanlab. He says that the key quality indicators for good ftheta objective are a low field curvature and a large imaging field. To ensure the best performance for various applications, intensive collaboration with our suppliers begins often before a scanning solution is designed. Early on, simulations can be used to assess performance when combined with specific scan head. In our laser laboratories, we test scanning lens samples to verify properties such as the transmission of laser wavelengths, the quality and homogeneity in the working plane, or the distortion correction.
Scanlab integrates scanning lenses by optimizing the mechanical mounting of ftheta lens in its various scan heads. Merkt says that it is crucial to meet the design mirror distances in order for best imaging quality as well as a large enough field size. “Another aspect is the distortion correction derived from the optical models of scanning lenses, and to integrate that correction into the control scheme for the scan system.”
Scanlab varioSCAN and excelliSHIFT are examples of z-shifters that can be used to create a three-dimensional scanning volume. 4). The z-axis can move the focus along the path of the beam and thus shift the working plane either above or below that defined by the lens. In this situation, a more complex 3D correction is required for the scan-head to control the laser focus in the desired XYZ location.
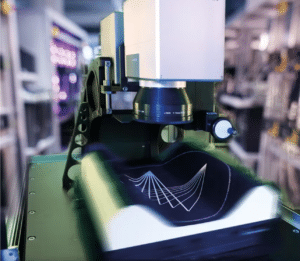
F-theta lenses keep laser-scanning nice and linear
Merkt notes that while the spot created by an ftheta lens is positioned in the same plane as the ftheta condition, the scan mirrors can compensate for deviations.
Scanlab systems cover wavelengths from 193nm to 10,6um. The examples can only show a small fraction of the processes that f-theta lens are capable of. Scanning speed is crucial in many laser marking processes, especially at low power levels. In some applications, CO 2 lasers can be focused using simple scanning lenses. This results in spot sizes as small as a few hundred nanometers.
Contrary to the first example of plastic welding, diode lasers can join transparent and opaque parts with moderate power. In most cases, the size of the image is large, and long focal lengths will be needed. The size of the spot is not as important.
Another application would be the laser welding of steel using high-power fibers lasers that exceed 1 kW. The scan lenses must be designed for low absorption.
Merkt explains that in micromachining f-theta lens are used. Especially those with a shorter focal length. These lenses allow for the creation of small spots and fine engraving on a variety of substrates including micro-optics.
Merkt says that some customers combine the f-theta and scan head with diffractive elements to shape the spot on the image plane.
Related Posts
Four Types of Barcode Scanners
How useful was this post? Click on a star to rate it! Submit Rating As you found this post useful......
The Future of Driving Monitoring: Advancements in Vision Technology and Lenses
How useful was this post? Click on a star to rate it! Submit Rating As you found this post useful......